SAEKI’s Patented 3D Printing for Light, Translucent Designs
SAEKI’s patented 3D printing technology enables the creation of featherlight and translucent interior elements, offering endless possibilities for artistic installations. Experience the future of interior design through innovative, modular components.
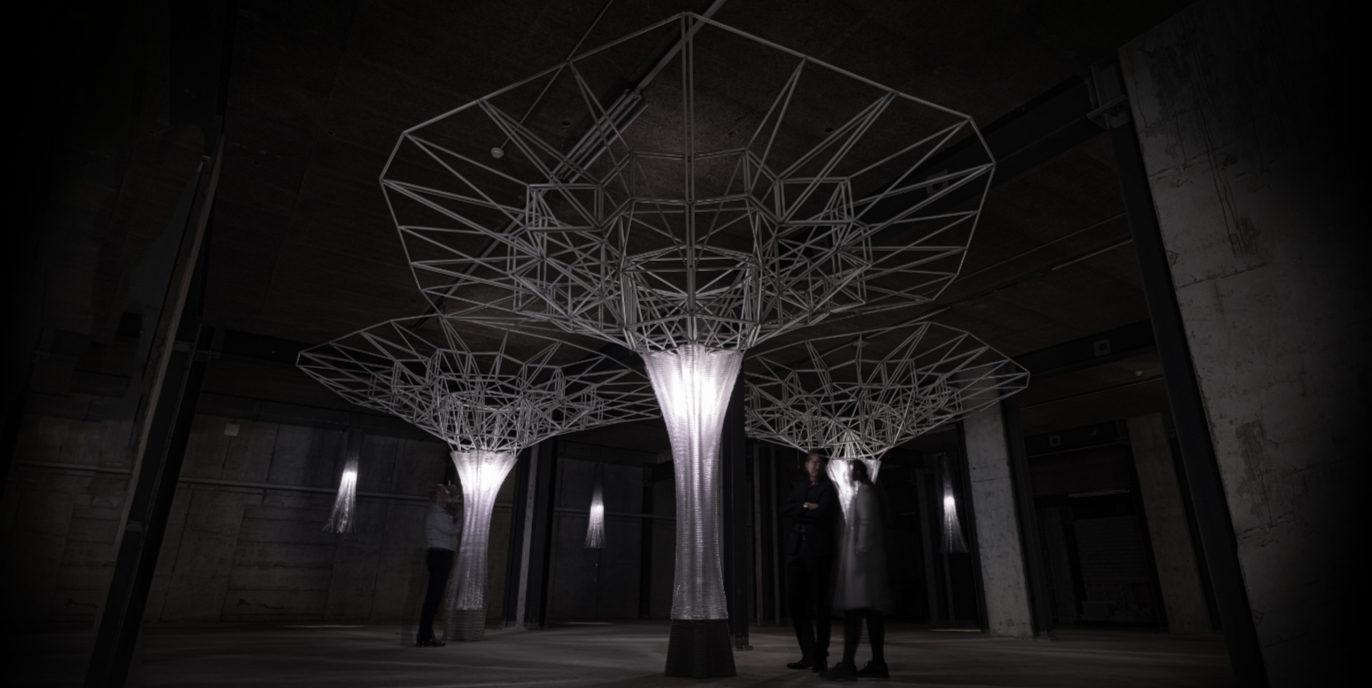
Introduction
As part of the Prōtóplasto exhibition, the MAS in Architecture and Digital Fabrication project at ETH Zurich, SAEKI contributed by producing the three load-bearing columns and nine 2.2-meter-tall chandeliers surrounding the space. The project was supported by the NCCR Digital Fabrication, funded by the Swiss National Science Foundation, and made possible through collaborations with Halter AG (space and event support), Castioni Kunststoffe (polymer tubing), and SAEKI (3D printing facilities). This article focuses on SAEKI's contributions to the project. For a complete overview, visit the full article by DBT ETH.
Prōtóplasto is an ultra-lightweight plastic media installation showcased at the innovation hub "Futurama" in Aargau, Switzerland. It represents a breakthrough in digital fabrication, combining novel 3D printing techniques to create a modular, lightweight structure. This project is driven by Hollow-Core 3D Printing (HC3DP), a patented technology developed by Matthias Leschok, co-founder and COO of SAEKI, during his doctoral studies at ETH Zurich under Prof. Benjamin Dillenburger. Through Prōtóplasto, we explore the untapped potential of plastics in architecture, demonstrating how innovative 3D printing methods can lead to efficient, sustainable, and adaptable construction solutions.
.jpg)
The Challenge
While plastics offer an excellent weight-to-strength ratio and are recyclable, they have been underutilized in architecture due to current manufacturing constraints. Specifically, standard 3D printing techniques often result in heavy, opaque structures, failing to leverage the original promise of lightweight, translucent plastic architecture. The goal of Prōtóplasto was to overcome these barriers and create an architectural-scale installation that demonstrates a new, efficient use of plastics through advanced digital fabrication.
.jpg)
The Solution
To address the project’s structural and fabrication challenges, SAEKI supported the 3D printing of ultralightweight columns using its patented HC3DP printing technology, providing not only the columns themselves but also the 3D-printed formwork for their bases.
HC3DP: Developed by SAEKI's co-founder and COO, Dr. Matthias Leschok, and exclusively licensed by SAEKI, this method extrudes tubular, hollow beads instead of solid ones, reducing material consumption while maintaining structural integrity. This innovation enables high build-up rates comparable to concrete extrusion while ensuring transparency and lightness.
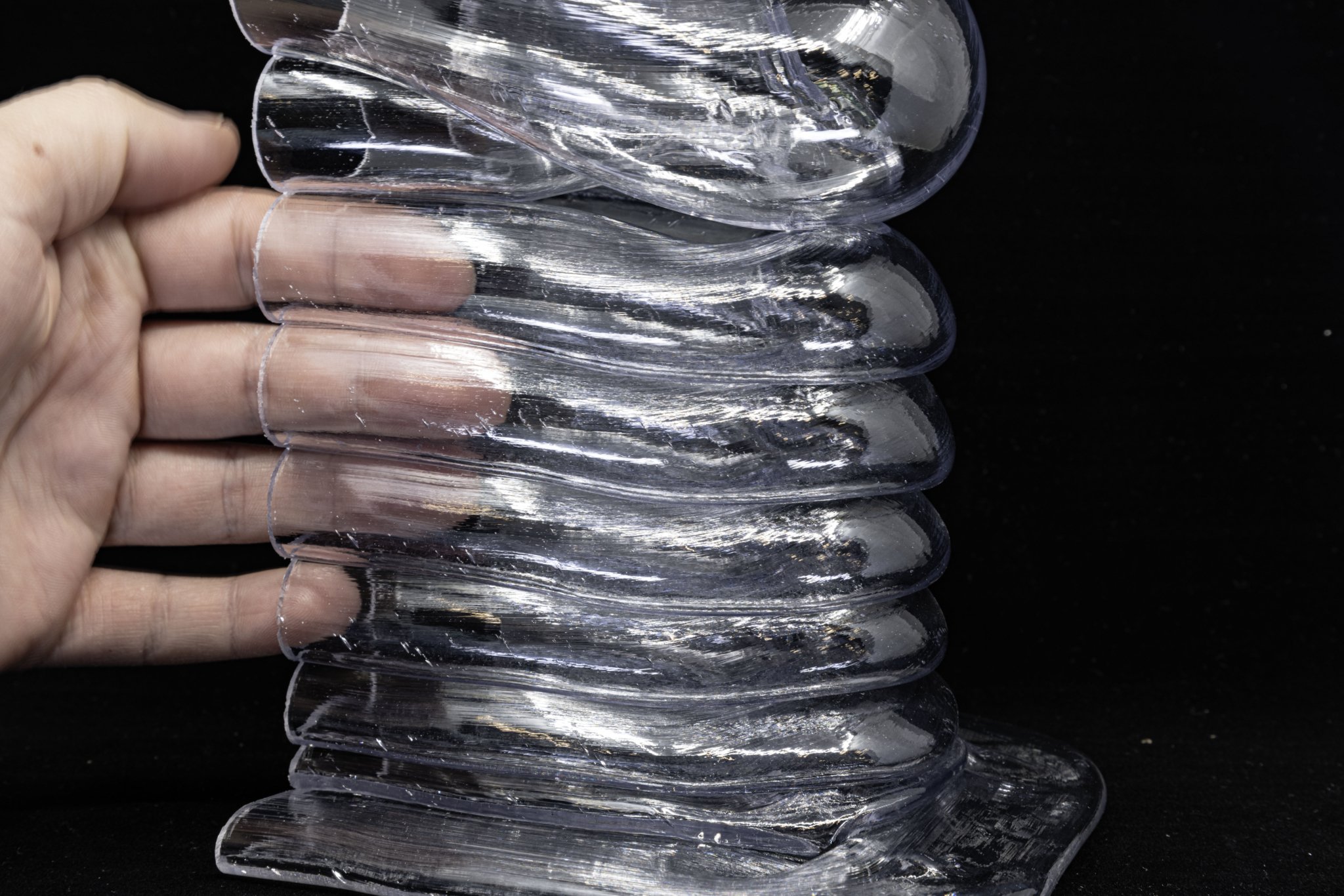
Implementation and Results
Prōtóplasto consists of modular mushroom columns, manufactured by SAEKI, and a lightweight roof system covering an area of 65 square meters, produced and assembled by ETH Zurich. The key results include:
- Efficient material use: The HC3DP method produced 2.2-meter-tall columns in just five hours, using only 20 kg of material per column—an 80% reduction in material use compared to traditional extrusion systems.
- Innovative roof system: The structure incorporates a modular radial space frame supported by ultra-light HC3DP columns. Custom 3D-printed joints, produced using HP's MultiJet Fusion technology, allow for dry, reversible self-interlocking connections.
- Ease of assembly: Each roof module weighs only 3.7 kg, enabling single-person assembly without additional supports. This lightweight and prefabricated approach minimizes construction waste and paves the way for future robotic and drone-assisted assembly techniques.
- Industry recognition: Industry professionals recognized Prōtóplasto as a significant advancement in digital fabrication, leading to its presentation at the prestigious Fabricate Conference.
Conclusion
Prōtóplasto is a testament to the potential of plastics in modern architecture when combined with innovative digital fabrication techniques. By leveraging HC3DP technology, this project demonstrates how lightweight, high-performance structures can be created with minimal material use and maximum efficiency. The successful implementation of Prōtóplasto opens new possibilities for sustainable and adaptable architectural solutions, challenging conventional perceptions of plastic in construction.
To learn more about the science and engineering behind HC3DP, read the open-access paper Large-scale hollow-core 3D printing (HC3DP): A polymer 3D printing technology for large-scale ultralightweight components.
How Can HC3DP Transform Your Next Project?
SAEKI is proud to offer this patented HC3DP technology to its customers, enabling the development of cutting-edge, lightweight architectural solutions. Whether you want to explore innovative construction methods, reduce material consumption, or push the boundaries of 3D printing in architecture, SAEKI is here to help. Contact us to discover how HC3DP can transform your next project.
Prōtóplasto team
Dr. Matthias Leschok, Dr. Marirena Kladeftira, Nik Eftekhar
Supporting technicians
Tobias Hartmann, Philippe Fleischmann, Heinz Richner, Jonathan Leu, Michael Lyrenmann