Enabling Precise Precasting for the World’s Tallest 3D-Printed Tower
Discover how SAEKI’s 3D-printed formwork enabled the construction of the world’s tallest 3D-printed tower. SAEKI provided 53m² of custom 3D-printed reusable formwork for the precasting of 64 concrete elements.
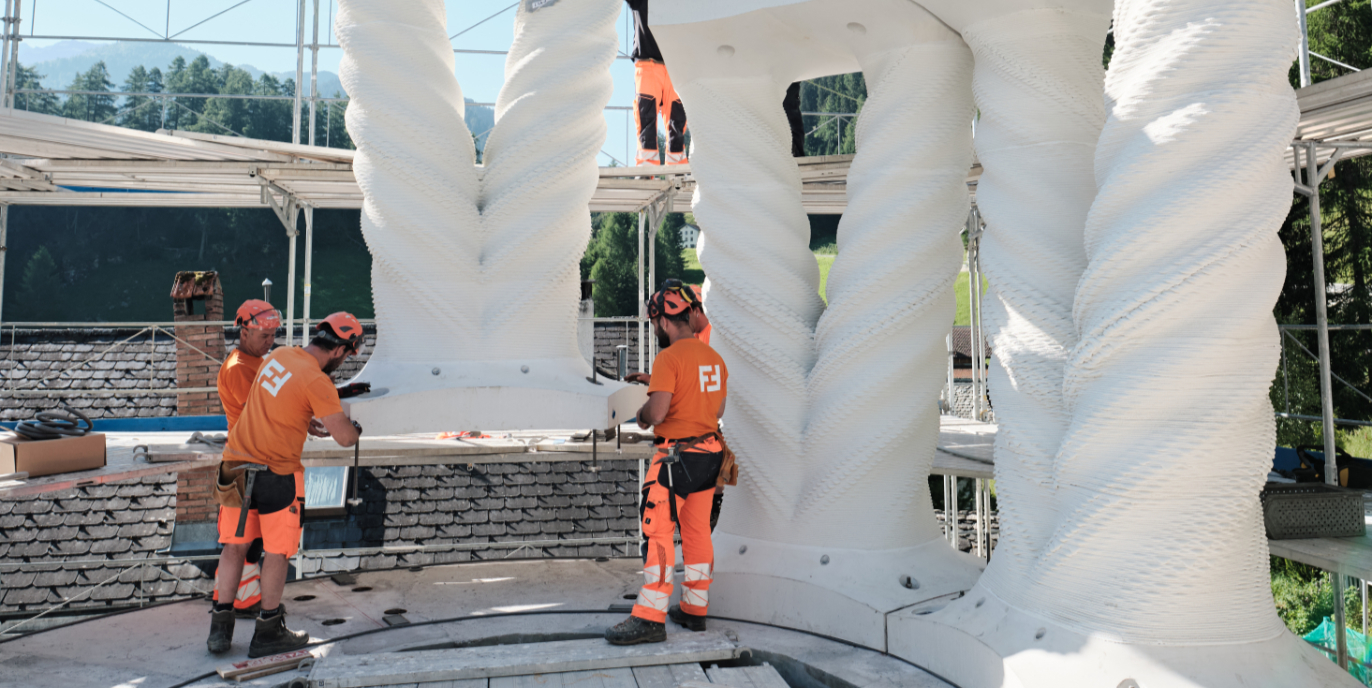
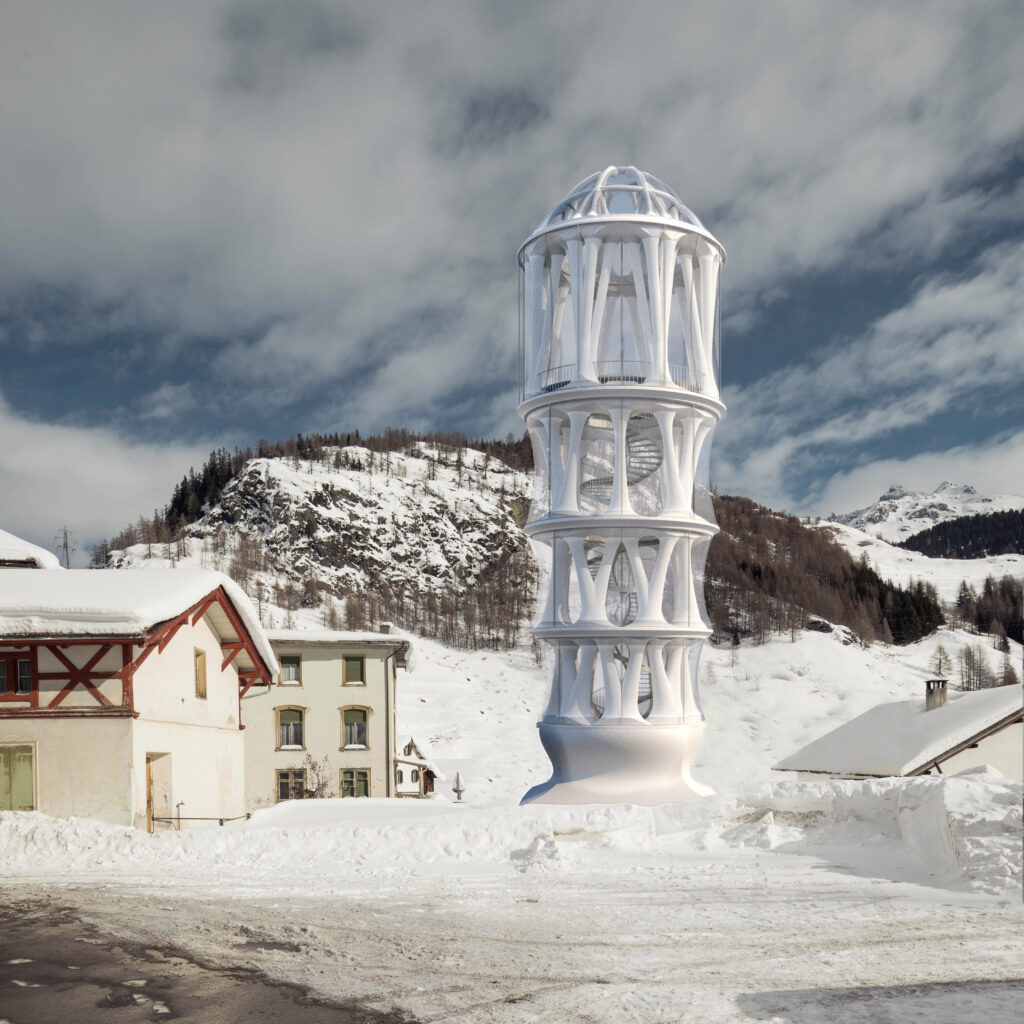
Introduction
Nova Fundaziun Origen, a cultural foundation based in the Julier Pass region of Switzerland, initiated the Tor Alva (White Tower) project to revitalize the alpine village of Mulegns. The tower is intended as both a cultural beacon and an architectural marvel, designed to inspire visitors, host performances, and highlight the transformative potential of computational design and digital fabrication in modern construction.
Tor Alva, a pioneering 30-meter-tall structure in Mulegns, is set to become the world’s tallest 3D-printed building, with completion anticipated in the spring of 2025. The tower’s unique design features 32 3D-printed columns that define its structural and aesthetic character, marking a milestone in architectural innovation. This project required an unprecedented approach to constructing the formwork for the base and capital of the load-bearing columns. SAEKI provided a transformative solution to this challenge by leveraging advanced 3D printing techniques, redefining traditional concrete formwork manufacturing processes.
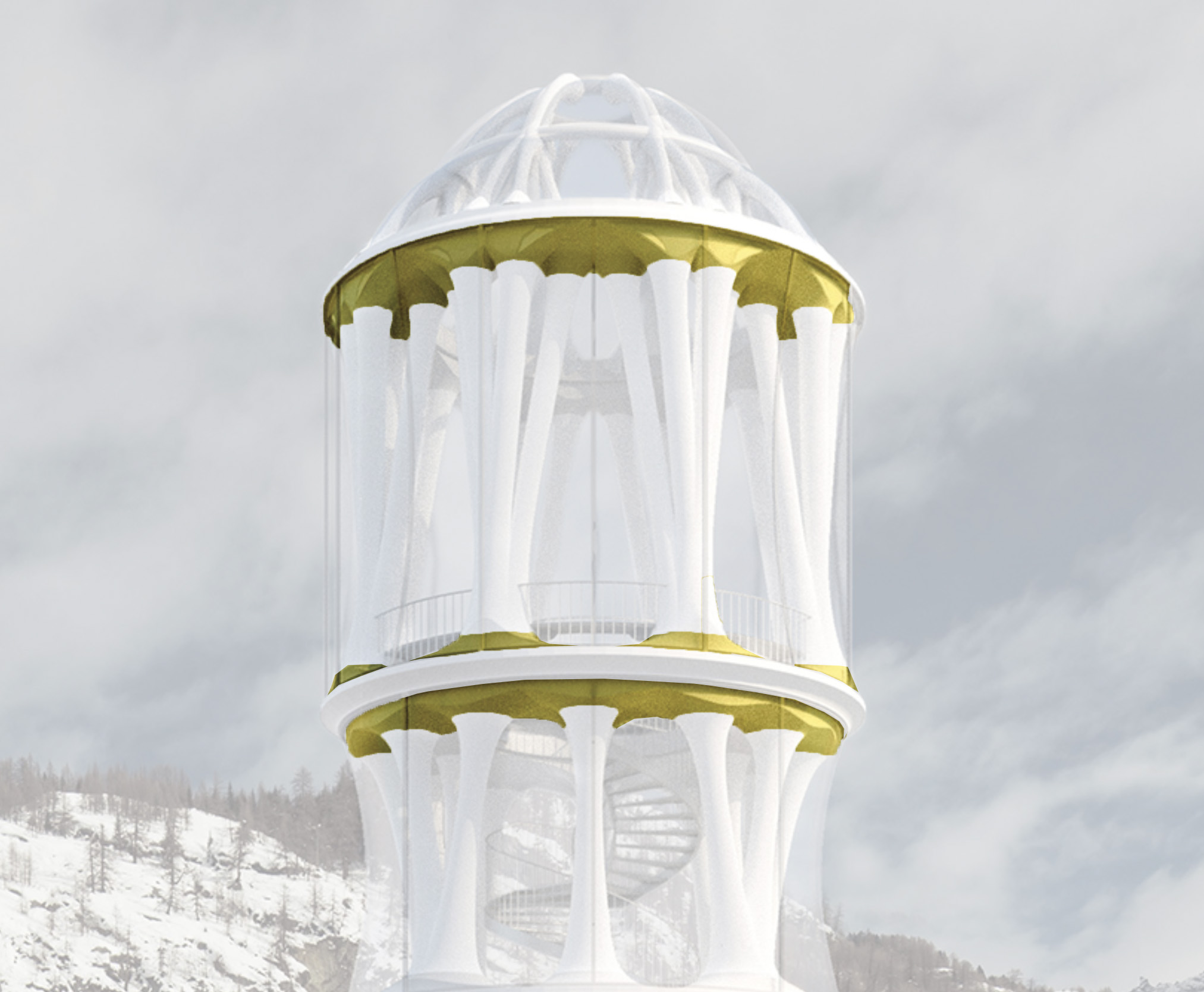
The Challenge
Traditionally, concrete formwork for non-standard designs are produced using methods like CNC milling of wood or foam. While effective for certain applications, these methods come with significant limitations:
- High costs & material waste: CNC milling involves the removal of material from solid blocks, generating substantial waste and increasing production costs.
- Composite formwork: To enable stripping, traditionally manufactured formwork almost always has to be coated (e.g. epoxy resin), which has a negative impact on recyclability.
- Limited reusability: Such formwork have only a limited reusability, which contributes to inefficiencies, particularly for projects requiring repeated casting of complex designs.
- Design constraints: Traditional methods struggle to accommodate intricate or non-linear geometries, which are increasingly demanded in modern architectural designs. Material-optimized designs are often simplified or even discarded.
For the Tor Alva project, the architectural vision required intricate column bases, and capitals that could support both structural loads and seamlessly blend into the 3D concrete printed columns. The solution had to address these challenges while ensuring precision, repeatability, and sustainability.
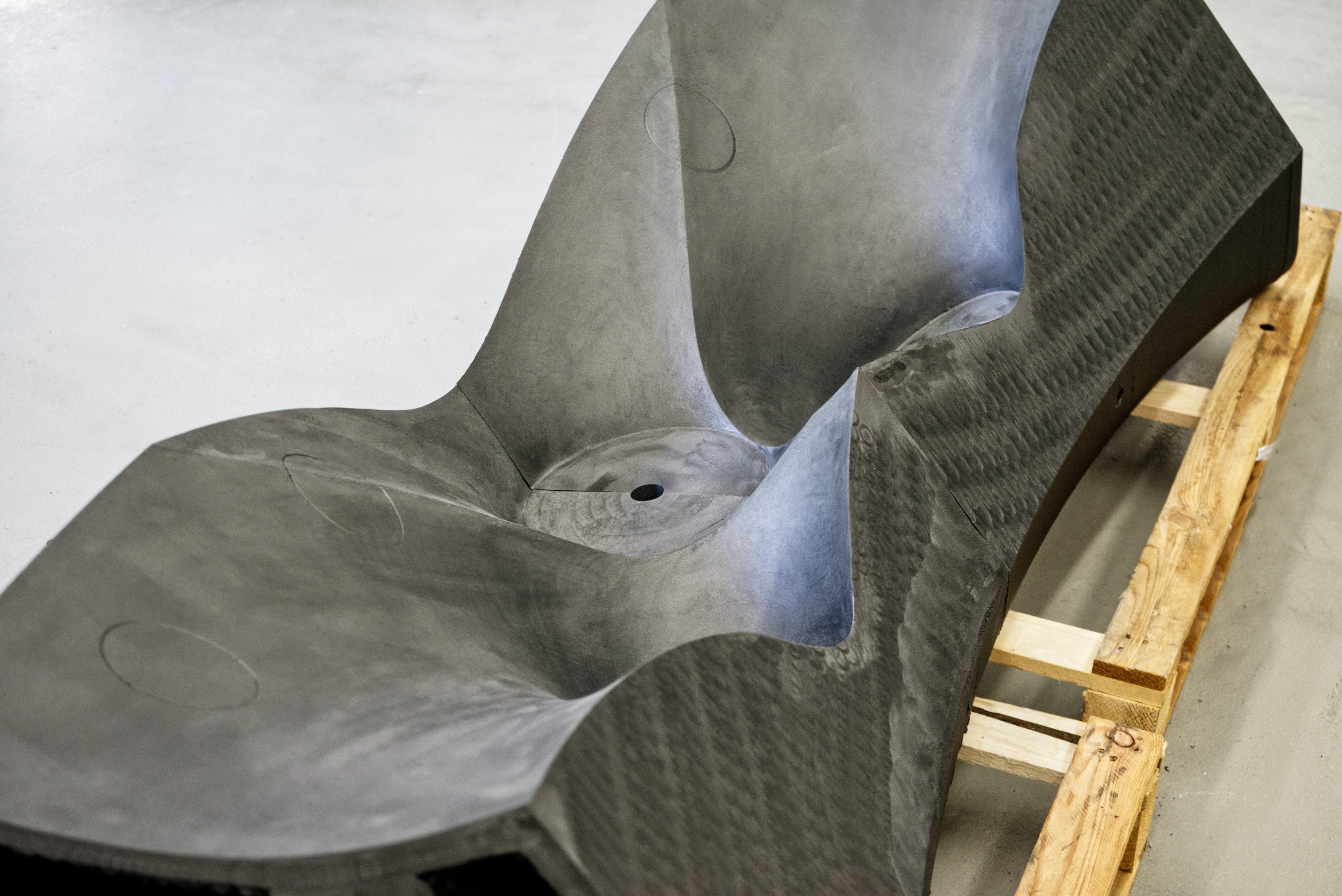
The Solution
SAEKI’s innovative approach revolutionized the production of concrete formwork by combining cutting-edge 3D printing technology with practical engineering expertise. Our solution offered the following advantages:
- Custom 3D-Printed Formwork: Using advanced polymer-based 3D printing, SAEKI created formwork tailored to the unique geometries of the column bases and capitals. Unlike traditional milled formwork, these polymer-based forms are durable and reusable, reducing waste and overall costs.
- Enhanced Design Flexibility: Due to the unique production capabilities of SAEKI, ranging from 3D printing to CNC machining, we were able to create durable formwork elements with intricate details, such as alignment features with fair-faced concrete finishes.
- Repeatability and Efficiency: For each floor, a single set of formwork was sufficient to cast up to eight large-scale elements, each weighing over one tonne.
- Sustainability: The application of reusable formwork, made from recyclable materials and minimized waste aligns with the environmental goals of modern construction, contributing to a more sustainable building process. With all elements completed, SAEKI has begun recycling the used formwork, paving the way for the next project to take shape.
.png)
Implementation and Results
SAEKI delivered over 53 m² of custom 3D-printed formwork for the Tor Alva’s project. These formwork were used to cast the concrete bases and capitals, which later on were seamlessly integrated with the 3D-printed central columns. Key outcomes included:
- Precision and quality:The formwork achieved a high level of dimensional accuracy, ensuring perfect alignment and load distribution in the final structures.
- Cost-effectiveness: By reducing waste and enabling reuse, the solution lowered material and production costs compared to traditional methods.
- Architectural Achievement: The intricate column designs were realized exactly as envisioned, underscoring the synergy between cutting-edge technology and artistic expression.
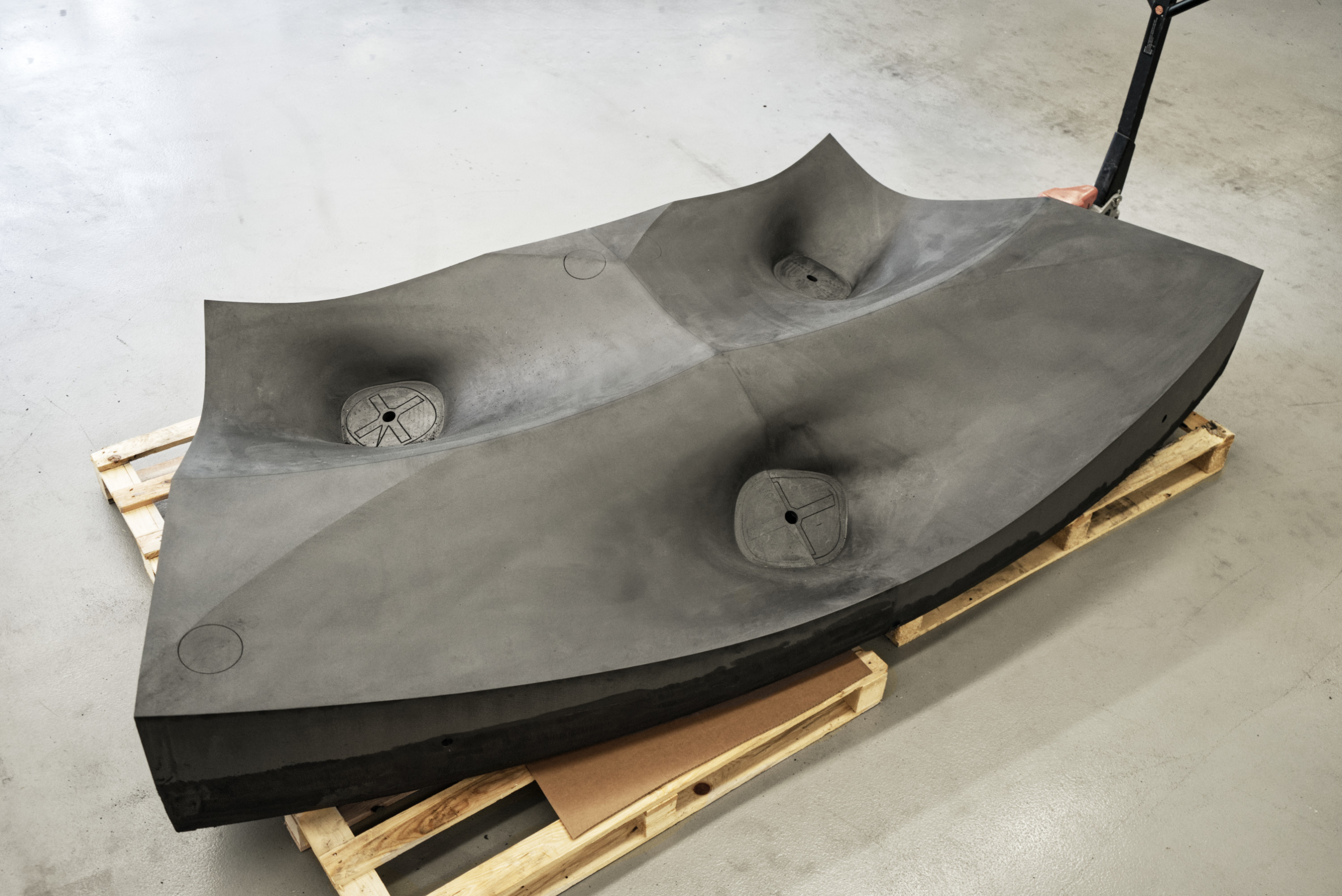
Conclusion
The Tor Alva project demonstrates the transformative potential of advanced 3D printing technologies in modern construction. By addressing the challenges of traditional formwork production, SAEKI provided a solution that was precise, efficient, and sustainable.
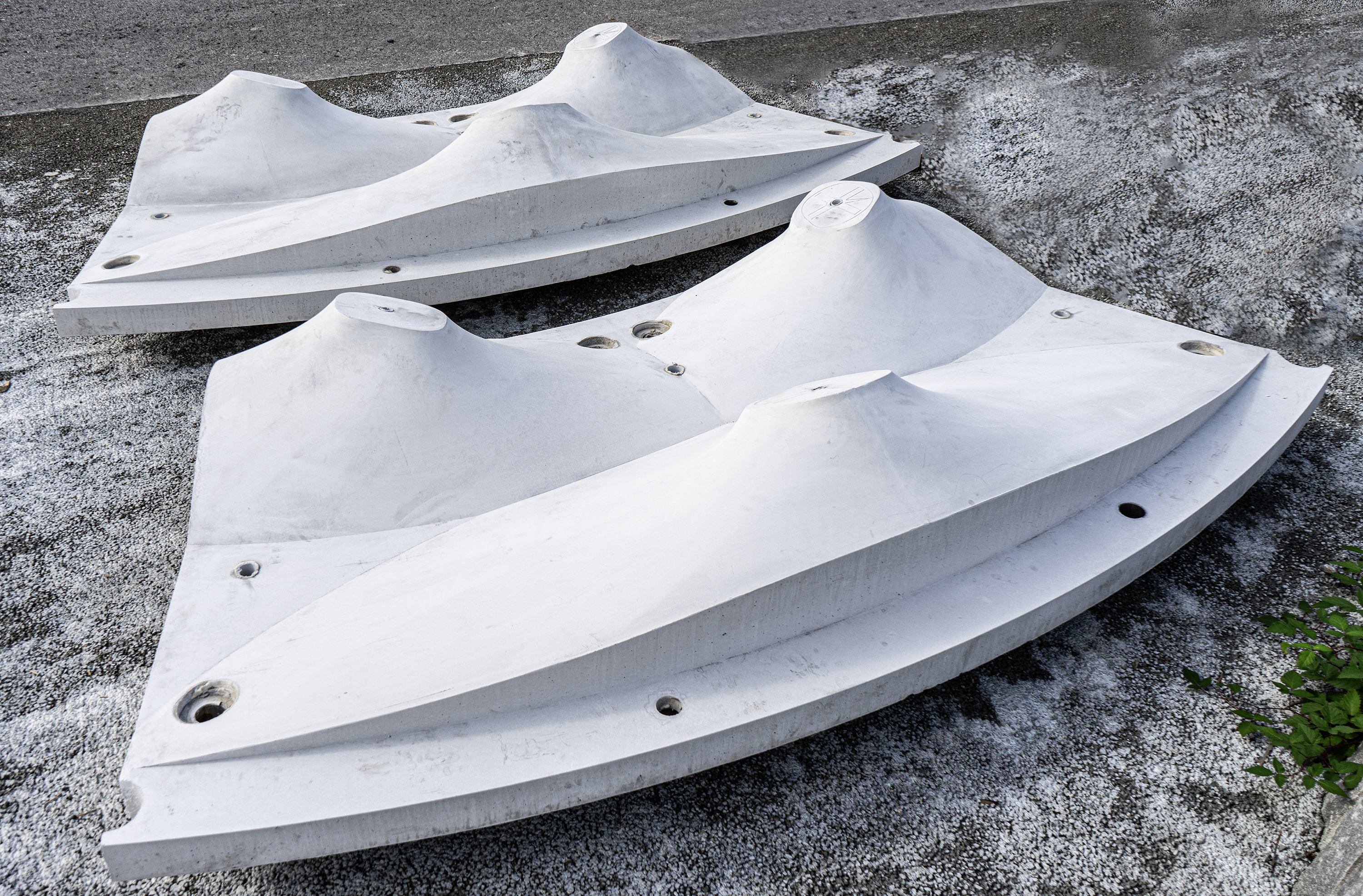
Ready to take your projects to the next level?
Get in touch with SAEKI to learn how we can help turn your creative concepts into reality.
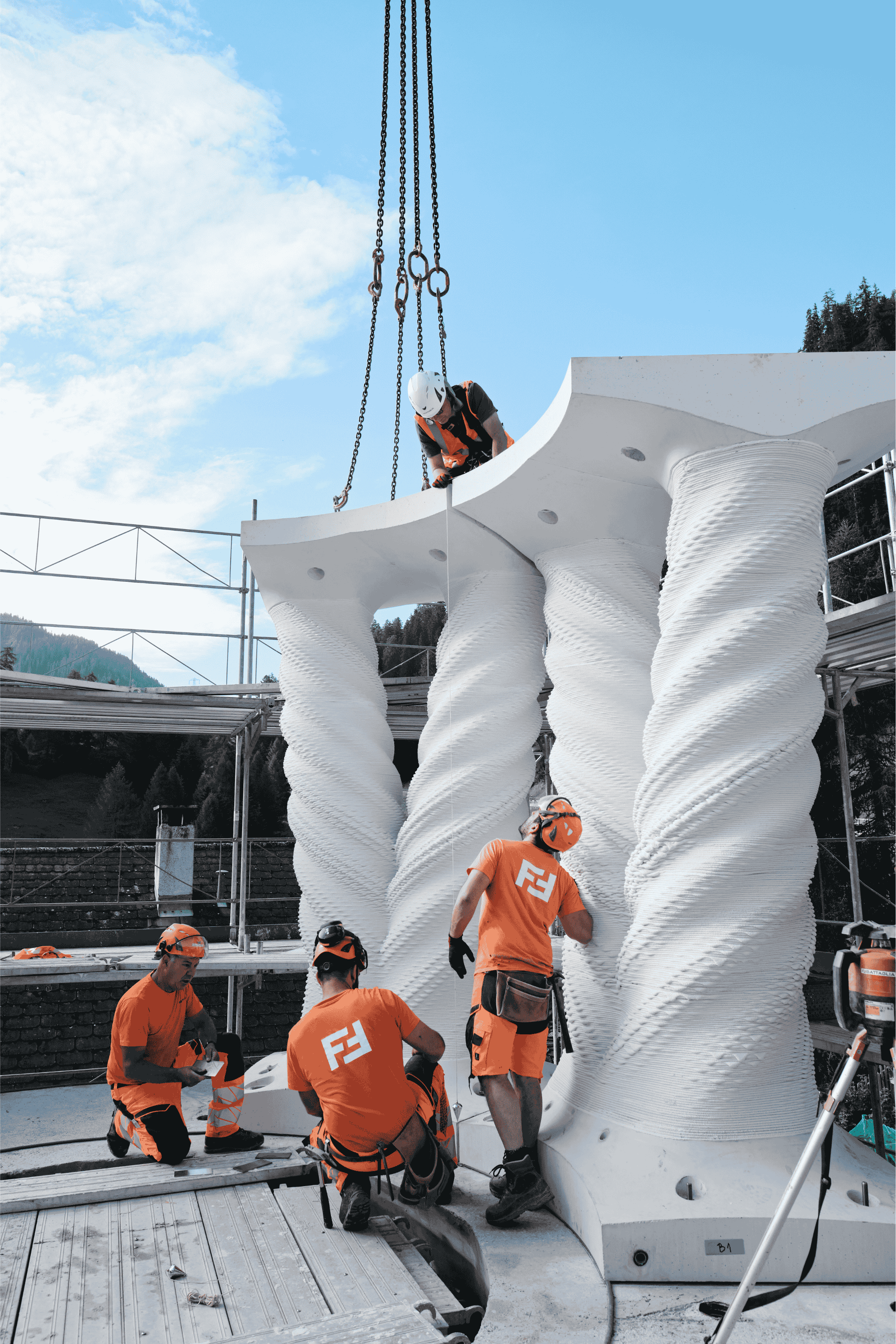
Project collaborators
The White Tower is the result of a close collaboration between the ETH Zurich, Conzett Bronzini Partner, Zindel United and the Nova Fundaziun Origen.
Architecture
Prof. Dr. Benjamin Dillenburger, Digital Building Technologies (DBT), Michael Hansmeyer
Team: Dr. Ana Anton (Research Lead), Eleni Skevaki, Che Wei Lin, Ming-Yang Wang, Lena Kitani, Su Huang, Dr. Konrad Graser (Project Coordination)
Structure
Prof. Dr. Walter Kaufmann, Institut für Baustatik u. Konstruktion (CSBD)
Team: Dr. Alejandro Giraldo Soto, Dr. Lukas Gebhard
Materials
Prof. Dr. Robert Flatt, Institut für Baustoffe (PCBM)
Team: Dr. Timothy Wangler, Dr. Lex Reiter
Geodesy
Prof. Dr. Andreas Wieser, Geosensors and Engineering Geodesy (GSEG)
Technicians / Robotic Fabrication Laboratory
Mike Lyrenmann, Philippe Fleischmann, Tobias Hartmann, Luca Petrus, Jonathan Leu
Partners
SAEKI (3D Printed Formwork)
Creabeton AG (Prefabricated Cast Concrete)
Invias (Zindel Uffer)
BASF (3D Concrete Printing Material)
Knauf (3DP Concrete Printing Material)
MESH AG (Robotic Rebar Technology)
Bieri (Membrane-façade)
Aalborg White (Cement)
Almatis (Accelerator)
Support
ETH Foundation Partnership Council for Sustainable Construction
Innosuisse SNSF
NCCR Digital Fabrication SNSF
For more details on the White Tower project, please visit the official White Tower project website: https://www.tor-alva.ch/