3D-Printed Formwork for Ribbed Slabs
Learn how SAEKI’s 3D-printed formwork enabled precise, sustainable on-site casting of bespoke concrete slabs. Our advanced technology and recyclable materials deliver cost-efficient, high-quality, fair-faced concrete finishes.
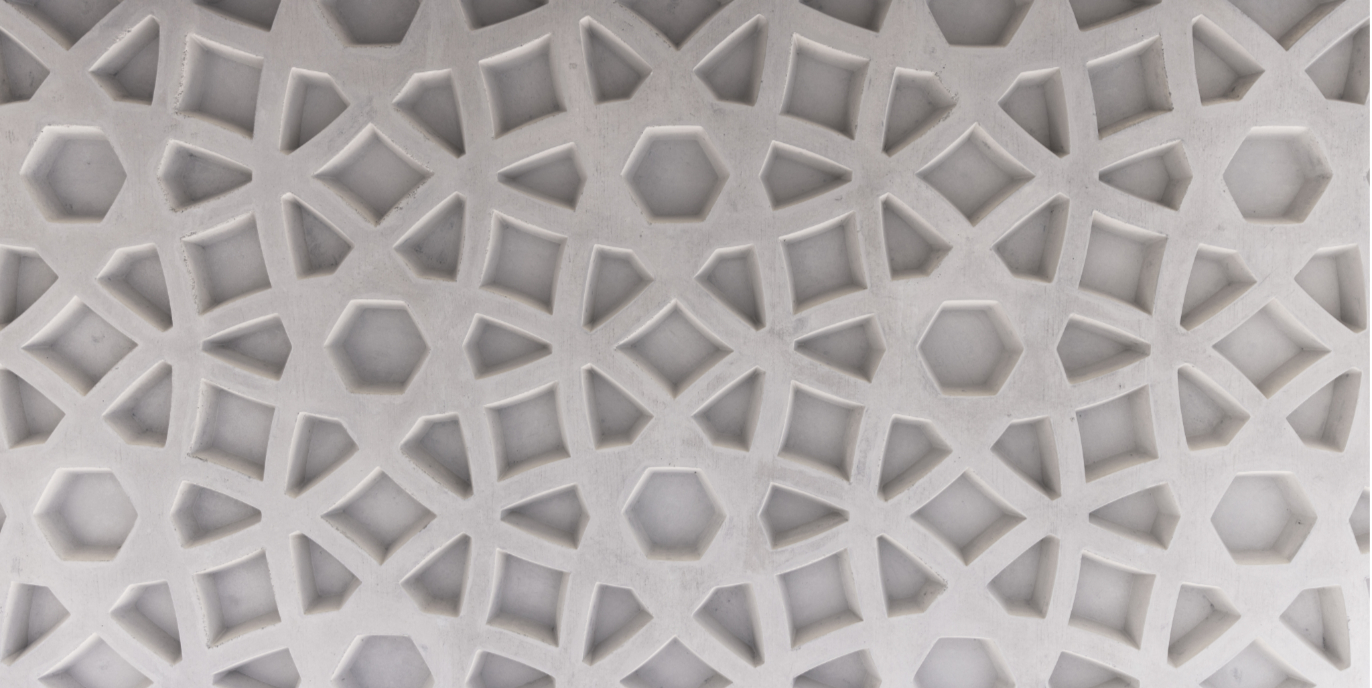
Introduction
Achieving high precision, cost efficiency, and sustainability in concrete casting is a major challenge for modern construction projects. For bespoke designs, traditional formwork solutions often require extensive manual labor, generate significant material waste, and lack flexibility. SAEKI addressed these challenges holistically by automating the design-to-production process of custom-made formwork elements.
This case study explores how SAEKI’s innovative technology enabled the on-site casting of a bespoke bicycle shelter, combining digital workflows, recyclable materials, and large-scale 3D printing techniques.
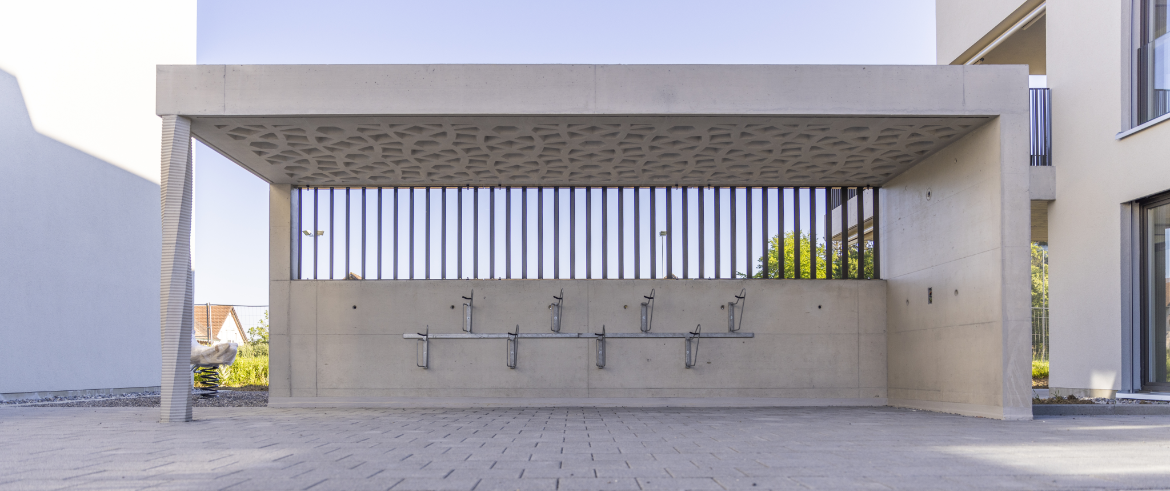
The Challenge
The project aimed to construct an aesthetically refined bicycle shelter made from concrete, using a ribbed slab design, and a custom-shaped column. The key challenges included:
- Digital Workflow Integration: The entire planning and execution process relied solely on a digital information flow — no traditional production drawings were printed or used on-site. This required a seamless connection between design, production, and construction workers.
- On-Site Concreting Risks: 3D-printed concrete formwork has yet to be widely adopted for on-site casting due to challenges related to high hydrostatic pressures and limited structural stability.
- Structural Optimization: The ribbed slab design required careful structural engineering to maintain strength while minimizing material usage. Hidden ledgers were integrated into the slab to compensate for reduced structural height, eliminating the need for conventional reinforcement within the ribs.
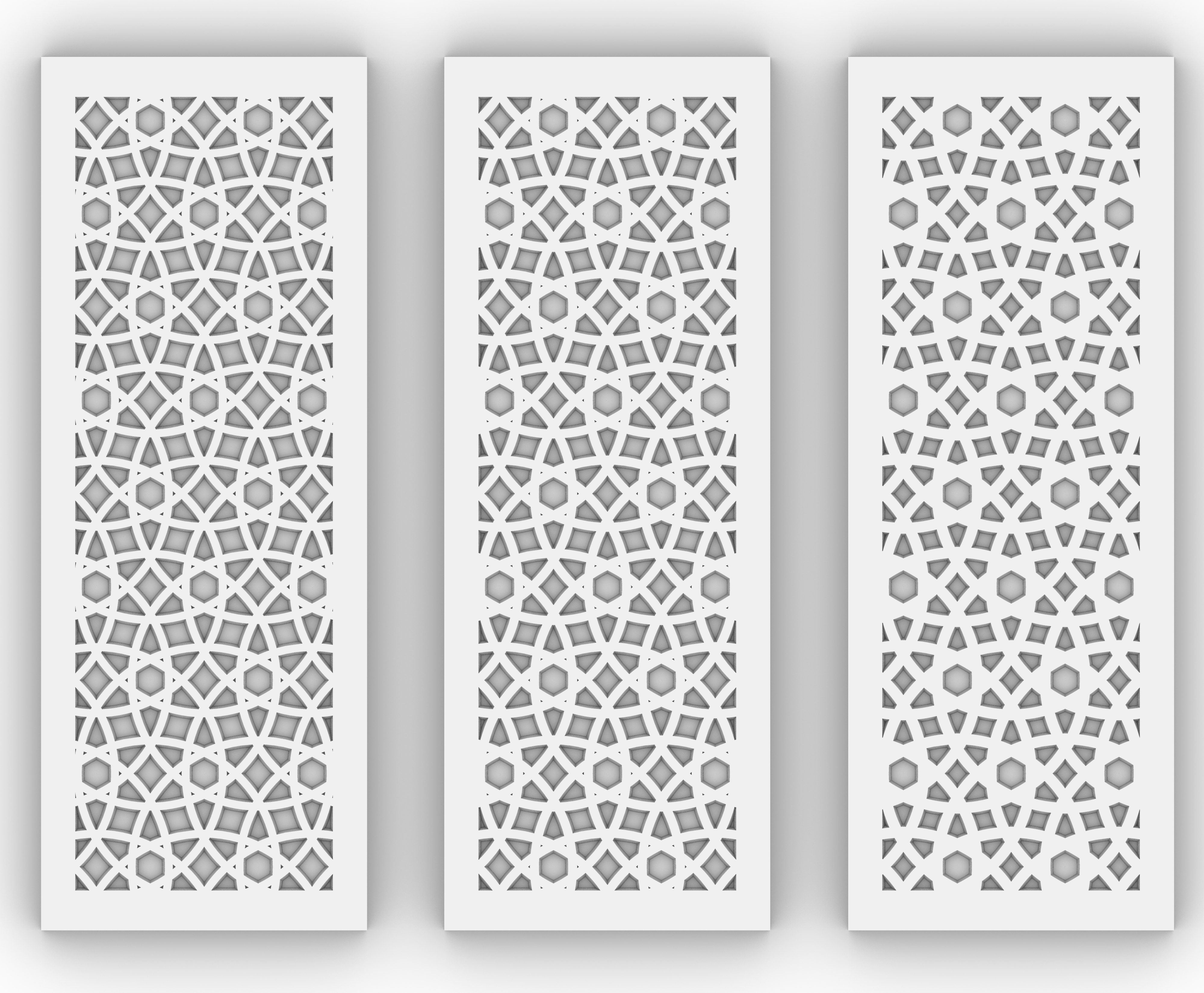
The Solution
SAEKI leveraged its 3D printing technology to manufacture precise and reusable formwork components, addressing both the technical and sustainability challenges of the project. Key aspects of the solution included:
- Parametric 3D Design: The digital workflow was fully integrated with KMP Architektur AG’s parametric 3D model, allowing rapid iterations without reprogramming for each design adjustment. This significantly accelerated the prototyping and production phases.
- Robustness: SAEKI established trust through rapid prototyping cycles in collaboration with Notter Hochbau AG, delivering robust and durable formwork with leak-free connections and precise alignment features.
- 3D-Printed Formwork for Ribbed Slabs and Column: SAEKI produced 3D-printed formwork inserts for the ribbed ceiling and a fully 3D-printed formwork for a bespoke 2.4-meter-high column. After 3D printing, the formwork elements were CNC milled to achieve fair-faced concrete quality and precise connection detailing.
- High-Performance Materials: SikaBiresin® TP103 was used to meet the demanding thermal and mechanical requirements. This recyclable plastic ensured dimensional stability and durability, making it ideal for on-site use.
- Collaboration with Industry Leaders: The project was executed in partnership with the BauCircle. The BauCircle consists of the Notter Hochbau AG, which is responsible for on-site construction; the NCCR Digital Fabrication for consulting; the Crinera GmbH for project management; and IKON Ingenieure AG for the structural calculations.
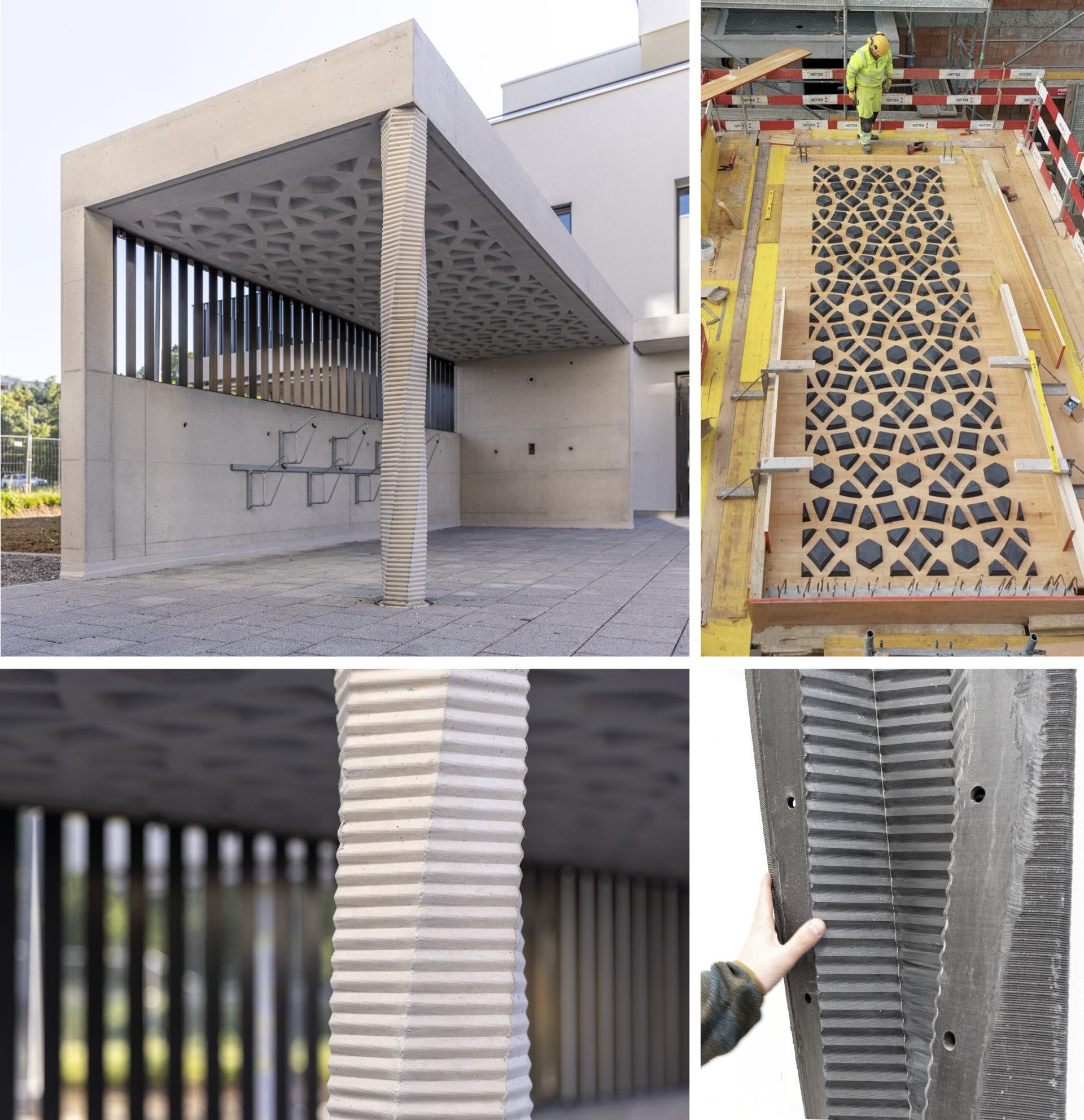
Results and Impact
- Cost-Efficient Customization: The 3D-printed formwork allowed for a high degree of customization without the excessive costs associated with traditional manufacturing of non-standard formwork.
- Sustainable Material Use: The formwork was designed for reusability, and after the project's completion, the used elements were recycled for future applications.
- Seamless Digital Execution: The parametric model-based workflow eliminated the need for traditional CAD exchange, enhancing coordination and reducing the risk of errors.
- High-Quality Concrete Finish: Enabled by SAEKI’s precision manufacturing and CNC finishing, the final structure met the highest standards of fair-faced concrete quality.
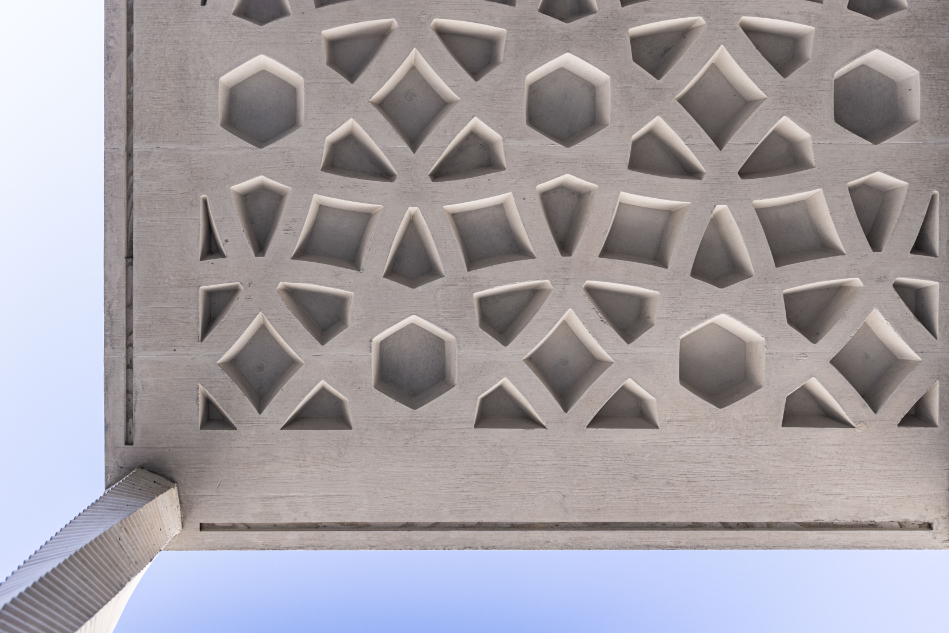
Conclusion
By integrating parametric design, 3D printing, and sustainable materials, SAEKI successfully delivered a pioneering solution for this construction project, demonstrating a future-proof approach to architectural concrete casting. With the success of this project, SAEKI continues to push the boundaries of digital manufacturing, offering innovative solutions for the construction industry.
Ready to take your projects to the next level?
Get in touch with SAEKI to learn how we can help turn your creative concepts into reality.