3D-gedruckte Schalung für gerippte Platten
Erfahren Sie, wie die 3D-gedruckten Schaltungen von SAEKI das präzise und nachhaltige Giessen massgeschneiderter Betonplatten vor Ort ermöglichen. Unsere fortschrittliche Technologie und unsere wiederverwertbaren Materialien sorgen für kosteneffiziente, hochwertige Sichtbetonoberflächen.
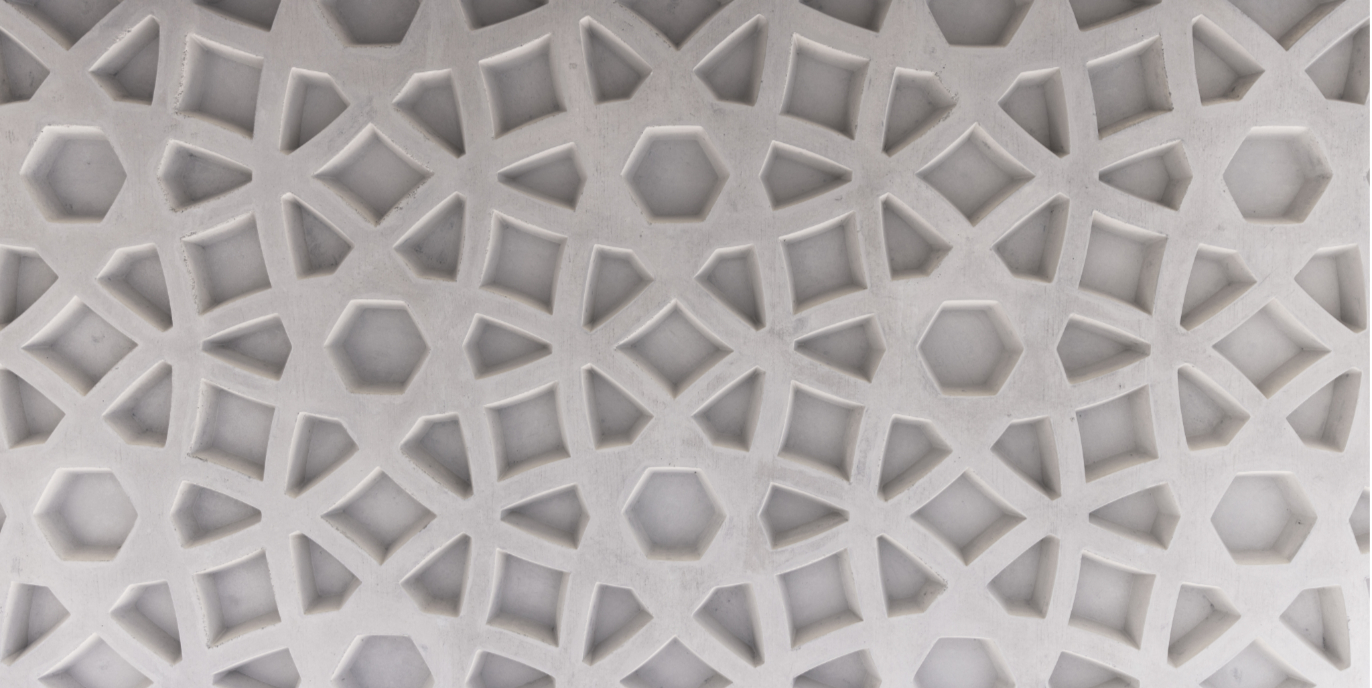
Einleitung
Hohe Präzision, Kosteneffizienz und Nachhaltigkeit beim Betongiessen sind eine grosse Herausforderung für moderne Bauprojekte. Herkömmliche Schalungslösungen erfordern bei Sonderanfertigungen oft einen hohen manuellen Arbeitsaufwand, erzeugen erheblichen Materialabfall und sind nicht flexibel genug. SAEKI hat diese Herausforderungen ganzheitlich angegangen, indem es den Prozess von der Planung bis zur Produktion von massgefertigten Schalungselementen automatisiert hat.
In dieser Fallstudie wird untersucht, wie die innovative Technologie von SAEKI das Giessen eines massgeschneiderten Fahrradunterstands vor Ort ermöglichte, indem digitale Arbeitsabläufe, wiederverwertbare Materialien und gross angelegte 3D-Druckverfahren kombiniert wurden.
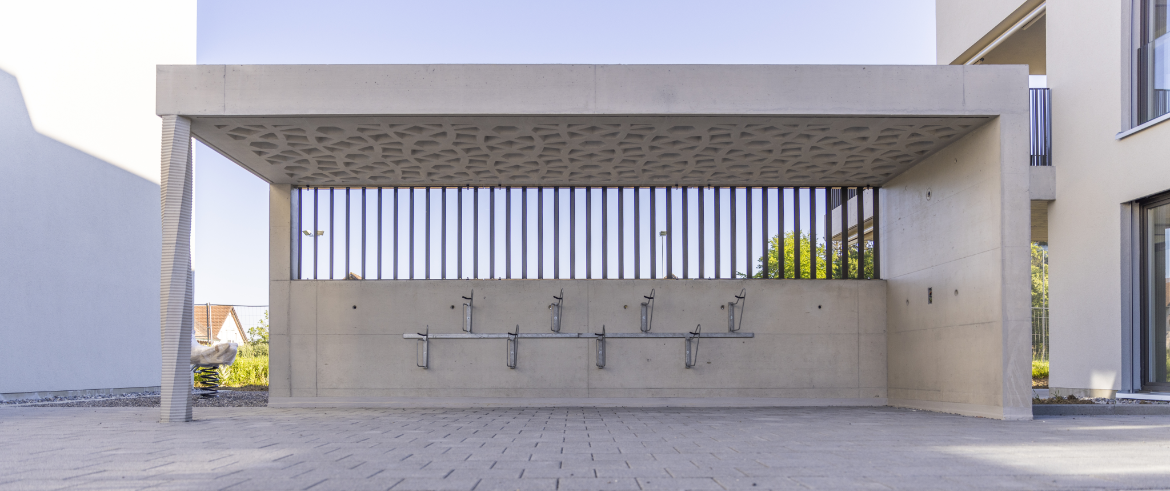
Die Herausforderungen
Ziel des Projekts war es, einen ästhetischen Fahrradunterstand aus Beton mit einer gerippten Platte und einer speziell geformten Säule zu errichten. Zu den wichtigsten Herausforderungen gehörten:
- Integration des digitalen Workflows: Der gesamte Planungs- und Ausführungsprozess beruhte ausschliesslich auf einem digitalen Informationsfluss - es wurden keine traditionellen Produktionszeichnungen gedruckt oder vor Ort verwendet. Dies erforderte eine nahtlose Verbindung zwischen Design, Produktion und Bauarbeitern.
- Risiken beim Betonieren auf der Baustelle: 3D-gedruckte Betonschalungen müssen noch auf breiter Basis für das Giessen auf der Baustelle eingesetzt werden, da sie aufgrund des hohen hydrostatischen Drucks und der begrenzten strukturellen Stabilität Probleme bereiten.
- Strukturelle Optimierung: Das Design der Rippendecke erforderte eine sorgfältige Statik, um die Festigkeit zu erhalten und gleichzeitig den Materialverbrauch zu minimieren. Versteckte Riegel wurden in die Decke integriert, um die geringere Bauhöhe auszugleichen, so dass keine konventionelle Bewehrung innerhalb der Rippen erforderlich war.
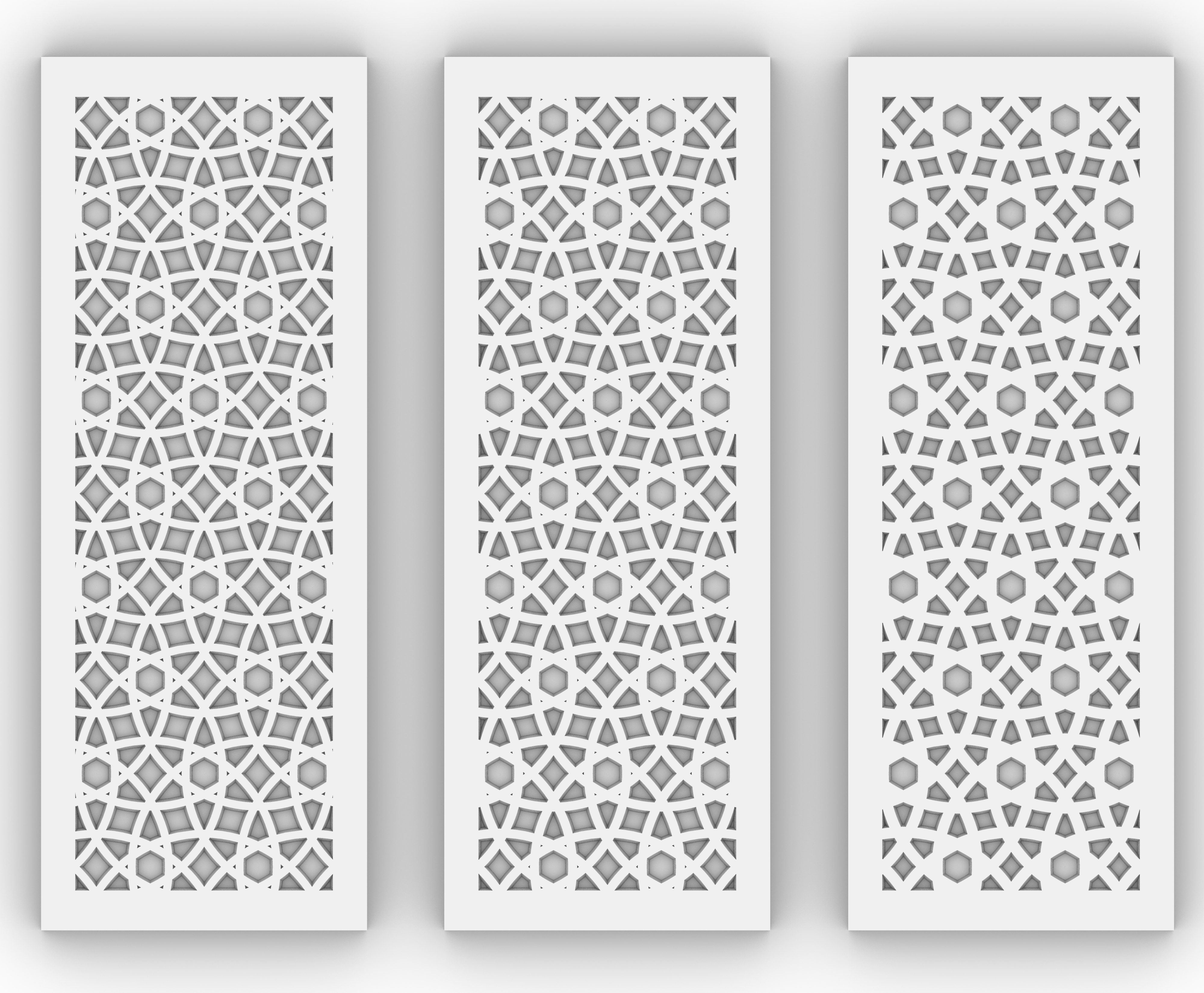
Die Lösung
SAEKI nutzte seine 3D-Drucktechnologie zur Herstellung präziser und wiederverwendbarer Schalungskomponenten, um sowohl die technischen als auch die nachhaltigen Herausforderungen des Projekts zu meistern. Zu den wichtigsten Aspekten der Lösung gehörten:
- Parametrische 3D-Konstruktion: Der digitale Arbeitsablauf wurde vollständig in das parametrische 3D-Modell von KMP Architektur AG integriert, was schnelle Iterationen ohne Neuprogrammierung für jede Designanpassung ermöglicht. Dadurch wurden die Prototyping- und Produktionsphasen erheblich beschleunigt.
- Robustheit: SAEKI hat durch schnelle Prototyping-Zyklen in Zusammenarbeit mit der Notter Hochbau AG Vertrauen aufgebaut und eine robuste und langlebige Schalung mit leckagefreien Verbindungen und präzisen Ausrichtungsmerkmalen geliefert.
- 3D-gedruckte Schalung für Rippendecken und Säulen: SAEKI produzierte 3D-gedruckte Schalungseinsätze für die Rippendecke und eine vollständig 3D-gedruckte Schalung für eine massgeschneiderte 2,4 Meter hohe Säule. Nach dem 3D-Druck wurden die Schalungselemente CNC-gefräst, um Sichtbetonqualität und präzise Anschlussdetails zu erreichen.
- Leistungsstarke Materialien: Um die hohen thermischen und mechanischen Anforderungen zu erfüllen, wurde SikaBiresin® TP103 verwendet. Dieser recycelbare Kunststoff gewährleistet Dimensionsstabilität und Langlebigkeit und ist damit ideal für den Einsatz vor Ort.
- Zusammenarbeit mit Branchenführern: Das Projekt wurde in Zusammenarbeit mit dem BauCircle durchgeführt. Der BauCircle besteht aus der Notter Hochbau AG, die für die Bauausführung vor Ort verantwortlich ist, dem NCCR Digital Fabrication für die Beratung, der Crinera GmbH für die Projektleitung und der IKON Ingenieure AG für die statischen Berechnungen.
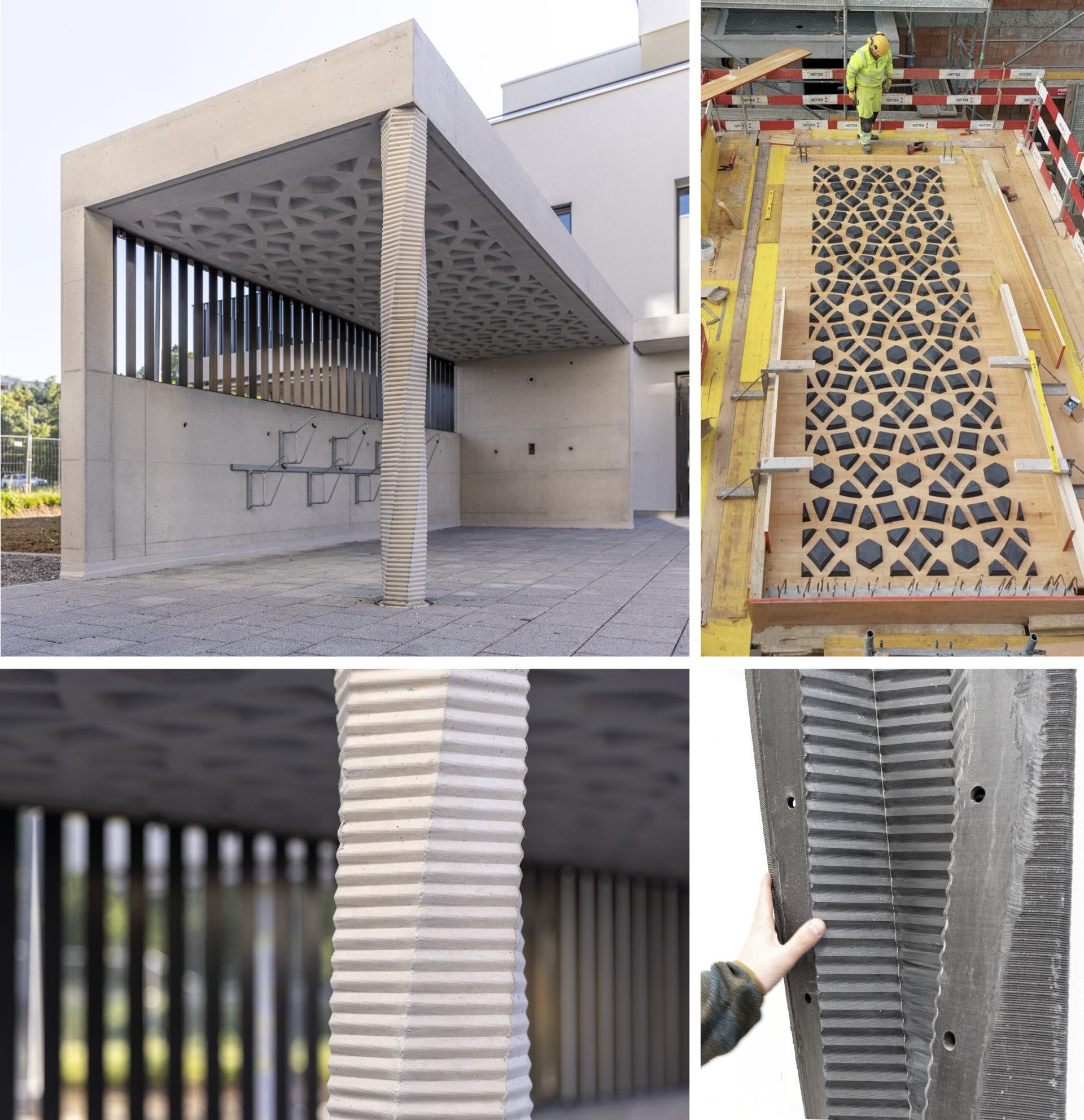
Umsetzung und Ergebnisse
- Kosteneffiziente Anpassung: Die 3D-gedruckte Schalung ermöglichte ein hohes Mass an individueller Anpassung ohne die übermässigen Kosten, die mit der herkömmlichen Herstellung von nicht standardisierten Schalungen verbunden sind.
- Nachhaltige Materialverwendung: Die Schalung wurde so konzipiert, dass sie wiederverwendet werden kann, und nach Abschluss des Projekts wurden die verwendeten Elemente für zukünftige Anwendungen recycelt.
- Nahtlose digitale Ausführung: Der parametrische, modellbasierte Arbeitsablauf machte den traditionellen CAD-Austausch überflüssig, was die Koordination verbesserte und das Fehlerrisiko reduzierte.
- Hochwertiges Beton-Finish: Dank der Präzisionsfertigung und CNC-Bearbeitung von SAEKI erfüllte die endgültige Struktur die höchsten Qualitätsstandards für Sichtbeton.
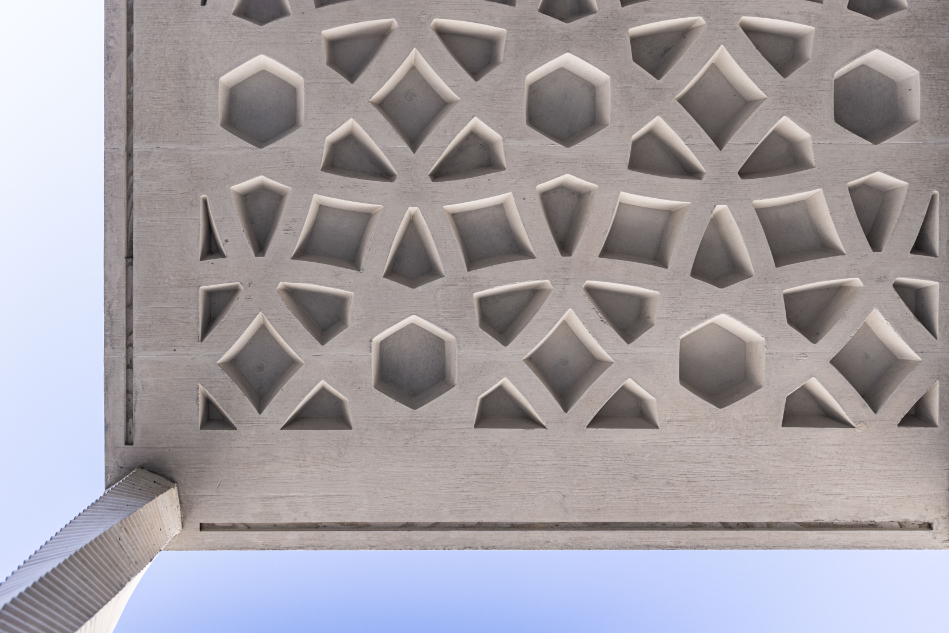
Fazit
Durch die Integration von parametrischem Design, 3D-Druck und nachhaltigen Materialien lieferte SAEKI erfolgreich eine bahnbrechende Lösung für dieses Bauprojekt und demonstrierte einen zukunftssicheren Ansatz für den architektonischen Betonguss. Mit dem Erfolg dieses Projekts verschiebt SAEKI weiterhin die Grenzen der digitalen Fertigung und bietet innovative Lösungen für die Bauindustrie.
Sind Sie bereit, Ihre Projekte auf die nächste Stufe zu heben?
Kontaktieren Sie SAEKI, um zu erfahren, wie wir Ihre kreativen Konzepte in die Realität umsetzen können.